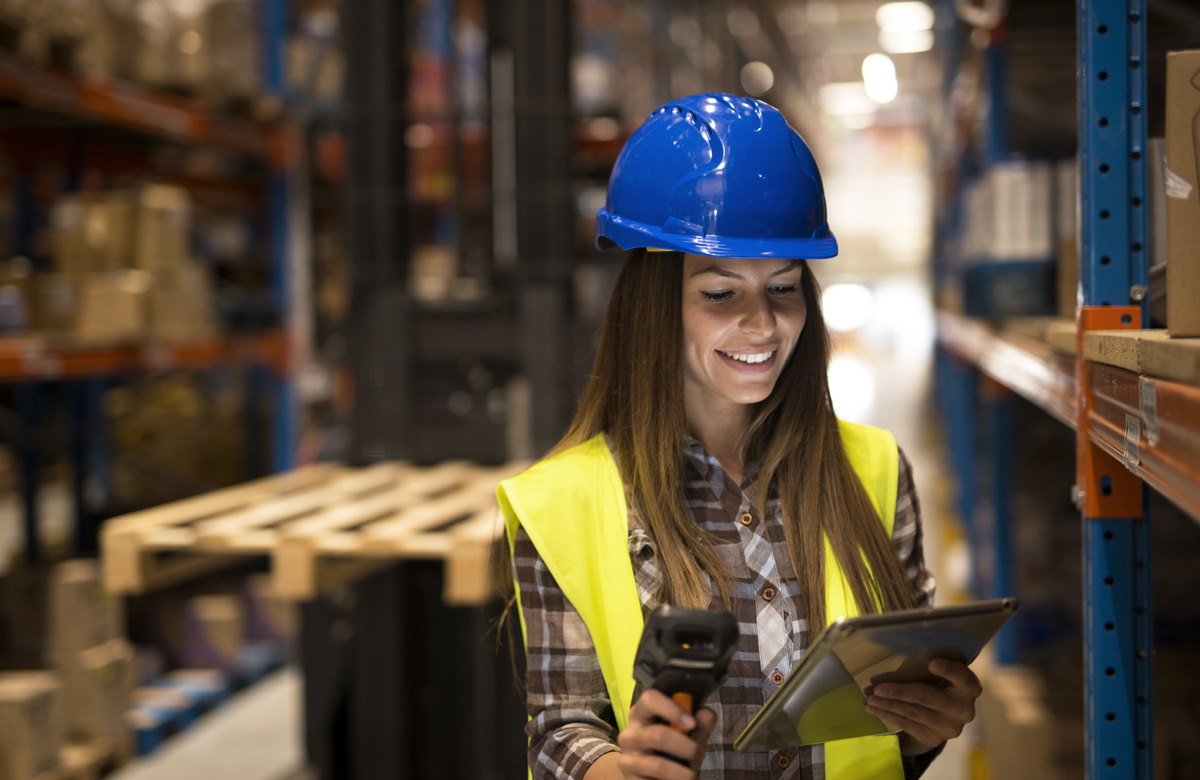
Why quality assurance is vital in the Logistics Sector
What is Quality Assurance ?
Quality assurance is where a companymakes thoughtful and planned efforts toeliminate the chances of mistakes andoverall improve their products and services. Experts in the quality assurance field will use a process-oriented approach and focusintensely on the prevention of defects at any point in the production and salespipeline. Quality control is often confused withquality assurance, but they are bothtechnically different things. Quality control involves efforts to detect defects, whilequality assurance involves efforts toprevent those defects altogether.
Preventing defects in the context of logistics can involve many different strategies, tools, and best practices. For the most part, logistics companies can usequality management systems,circumstance monitoring, and datacollection and analysis to stay on top of changes or mishaps that occur during transportation. We’ll break up some possible use cases for these tools into different relevant areas of logistics namely, perishables, marine shipping, and truck transportation.
Why is quality assurance so important for logistics ?
It’s no surprise that logistics is the most important aspect of facilitating a supplychain, no matter what industry. It’s alsovital to go through significant changes asmore and more disruptive solutions to quality monitoring pop up, namely in the form of software as a service. This can best ressful to keep up with, but it’s ultimately the best thing that could happen to the industry. With new solutions, it’s becoming easier to set up a continuous channel of communication and establish end-to-endvisibility through all aspects of the supplychain. Still, disruptive solutions are still disruptive.It’s the responsibility of the logistics companies to make sure the process of implementation is as smooth as possibleand ensure that the technology that is being adopted works correctly. Quality assurance is absolutely necessary in this situation to make sure companies in the supply chain don’t fall into madness andare working as optimally as possible.
Right now, we’re experiencing a major shift in which every area in the transportation world’s operational flow is utilizing technology to replace error-prone human activity. The days of holding up an easy-flowing channel are long gone, and the responsibility is now falling on software. This, of course, comes with its own set of issues. It only takes one glitch to put anentire supply chain at a halt. This is actually very dangerous territory. Marine cargo carriers may not be able to communicate with port authorities, gate passes won’t be accessed, payments will not process, orders won’t go through. Customers, clients, and brands could be affected. All of your sectors could be affected.
This is probably the biggest reason why quality assurance should be considered a mandatory practice. It’s important to ensure that a newly-implemented technology’s processes remain sophisticated. Extensive testing services must be utilized to provide complete visibility into the logistics operation workflow, from A to B.
This is the tough truth about perishable transport at every step of the supplychain, from warehouse to boat to truck to store, perishable items need to be in the right conditions to avoid spoilage.
Quality assurance and transporting perishables
Food spoilage is one of the main road blocks logistics companies deal with when it comes to transporting perishable items throughout the supply chain. Unfortunately, supply chains are responsible for around 40% of food waste in the United States something that will no doubt become more of an issue as the global population rises and food becomesmore valuable. Just as well, pharmaceutical companies need utmost quality assurance when it comes to transportation and en-route storage. Many different types of medications require storage at a certain temperature to maintain potency. If a truckis not properly air conditioned, massive batches of medications could be rendered useless.
So what can be done about this? To start, logistics companies need to start considering how they can improve overall quality assurance for perishable cargo andthe brands that produce them. There are afew ways to do this. Data logging
is currently on the rise as a major solution to perishable item spoilage. A data logger is a digital device that canrecord data over the period of a certain amount of time through the use of sensorsor built-in instruments. These devices have a wide range of uses, but can be particularly helpful in monitoring transportation conditions for products.
If a data logger can be used in conjunctionwith an analytics dashboard program (suchas a quality monitoring platform) and letteams know in real-time if there is adangerous dip or rise in temperature, thenthe relevant teams can remedy the issue before it results in food spoilage. Thus, quality is assured and food waste is prevented. Data logging, when using the right equipment, can be fairly easy to implement into marine and truck transportation as well. It’s certainly less disruptive than it used to be, which can be a real blessing tologistics companies who don’t want to deal with disrupting their supply chains.
How can quality assurancebe implemented in the logistics industry?
First and foremost, quality assuranceservices and strategies should involve diverse and extensive forms of testing. There’s simply no other way to make sure that all aspects of a logistics company’stech is working optimally. Here are a few forms of testing to consider, depending on your niche. Mobile device testing. In today’s age, notutilizing mobile frameworks and devices inthe logistics industry is a great way to fall behind competitors. Since a majority of users (stock teams, drivers, managers, etc.)will access logistics software through mobile devices and applications, it’s very important to invest in mobile testing. Mobile testing ensures that users at all areas of the supply chain can access relevant data and reporting software applications through their devices and enjoy a fluid, user-friendly experience thatonly improves productivity.
Cloud storage testing. Everybody in every industry is beginning to move towards cloud storage. It certainly makes sense why cloud storage has many great use cases for different businesses. But withthat migration comes a lot of potential problems. Cloud security is still evolving tobe the best it can be. And with such massive storage needs for a logistics company, it’s very important that the cloud is a safe and fully functional space for a business’s valuable data. Plus, the actual act of migrating data from physical storage to cloud can be a little difficult. Cloud testing can ensure a very smooth transition and can also help in improving security,latency, and overall performance.
Functionality testing. Logistics software needs to be multi-functional. Nobody wants to deal with a dozen or more different platforms when a company’steams can just get through the learning curve of one or two programs. Because of this, there is a lot of pressure on logistics software vendors to incorporate more and more features that can handle many different process flows. Functionality testing can thoroughly check whether the features of such bulky software are working properly for all of the company’s use cases. Performance testing. The supply chain can span cities, states, and even countries.That’s a hefty network to deal with, so it’sonly natural to implement performance testing. This type of testing ensures that a company’s software applications won’t crash or degrade during seasons of heavy activity. Performance testing and functionality testing often go hand in hand.
Security testing. Logistics companies deal with a heavy load of valuable (and of tensensitive) data. Security measures must be taken to make sure that data is safe through out all levels of the supply chain, especially since outside-of-premise mobile device use is becoming more of the norm. Security testing can ensure that security vulnerabilities are constantly being searched for and remedied.
That’s a lot of testing to take on. Luckily, you can outsource testing and monitoring services from quality assurance-focused businesses. Logmore can also aid in quality assurance for your logistics company. We specialize in the food and pharmaceutical niche and strive to reduce the two major issues these industries face in transportation spoilage and waste. We currently offer services that involve monitoring conditions in freight, such as temperature and humidity. We also provide business intelligence that specifically targets data logging so that food and pharma brands can identify issues (and fix them) as quickly as possible.